Solar proves a winner, delivering real savings to chicken growers
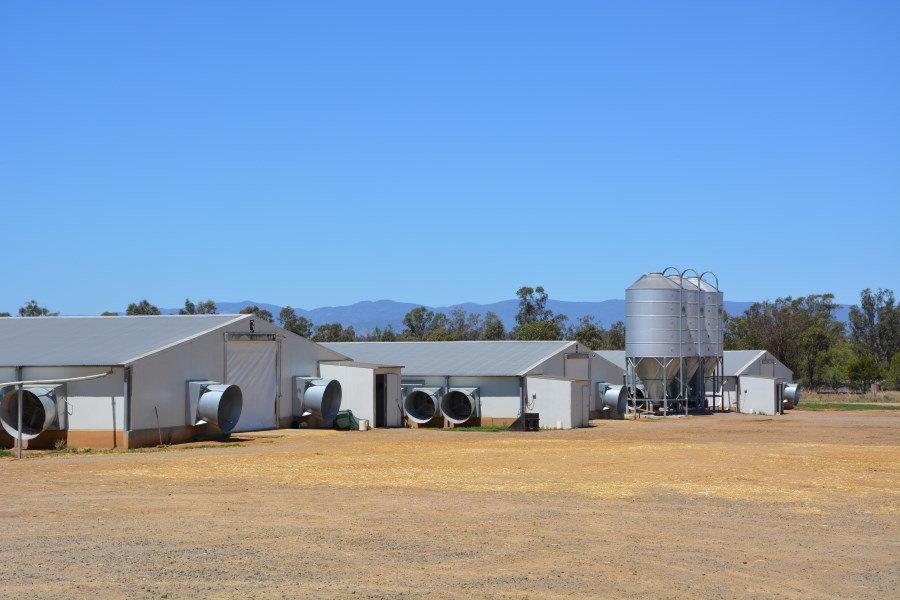
[Click here to download a PDF version of this information paper]
Poultry farmers run sophisticated sheds that automatically regulate temperature, air quality and light conditions. This can require a lot of power, especially during heat spells. Solar PV systems provide great value for chicken growers, as they maximise energy savings during hot and sunny days.
“I have built many sheds in my time and I have a fair idea about the quality necessary to support this business over a long time frame; however, with recent energy price rises and advances in energy technologies, NSW Farmers are helping me to understand what energy options will protect my margins, yet deliver the yields expected in our business.” Justin Roach, farm owner |
The area around Tamworth has become one of NSW’s primary locations for chicken production. Valdimah Park is a chicken meat farm about 30 minutes from the centre of town. Justin Roach, who runs the property, has been a successful chicken farmer for a number of years, and is interested in expanding his operation to keep up with the growing Australian demand for chicken (expected to double in the next 10 years).
Running hot and cold
Young chickens require high temperatures to stay healthy and grow quickly. Maintaining optimal temperatures in the ‘chicken hotels’ for the time that the animals are on-farm requires energy for heating and cooling.
Ideal temperatures for young chicks are over 30 degrees Celsius, which means sheds must be heated whenever a batch of newly hatched chickens arrives. As the birds get older, grow bigger and take up more space in the shed, requirements for ambient temperature lessen and the body heat of the birds is often enough, or more than enough, heat for the sheds. Ventilation systems are used, along with evaporative cooling pads on the walls of the buildings, to pull heat out of the sheds, provide fresh air for the birds and keep them from overheating.
Other energy requirements for poultry farmers
In addition to heating and cooling, chickens need fresh water, a constant supply of feed, and lights in the shed. Electricity is used to run the pumps for water, augers and conveyers for feed, and shed lighting. Overall, Justin’s operation is heavily reliant on large amounts of electricity and gas for heating – an extra cost for the often-cool countryside near Tamworth.
Reducing costs for electricity and gas
Justin’s farm is already one of the more efficient chicken-growing enterprises in the state, according to his customer/processor; still, there are opportunities to reduce current energy use within the sheds at Valdimah Park and to target optimal efficiency for any new sheds Justin builds.
Valdimah Park’s energy profile
Table 1: Valdimah Park’s energy source breakdown
NSW Farmers
The farm’s largest energy expense currently is for the gas used to heat the chook sheds in order to achieve optimal growth rates and weight gains across the standard six-week cycle.
Fan motors for ventilation are also a significant energy draw, accounting for the greatest proportion of electricity used on the Valdimah Park property.
Table 2: Valdimah Park’s energy use breakdown
NSW Farmers
Figure 1: Valdimah Park’s energy use by type and purpose
NSW Farmers
Cost reduction opportunities
At Valdimah Park, the NSW Farmers' Energy Team found the following energy-efficiency and cost saving opportunities.
Table 3: Full list of opportunities for Valdimah with 5 priority opportunities highlighted (note that ‘UI’ denotes ‘Under Investigation’)
NSW Farmers
Justin sat down with the NSW Farmers Energy Team in his site shed and nutted out the priority opportunities, considering ways to strip energy wastage from his current operation and the potential impact of this on his expansion plans.
The priority opportunities (marked with asterisks in Table 3) Justin plans to implement or investigate further are:
- Lighting upgrade: With lighting required for up to 16 hours a day, every day, there is a great business case for upgrading the lighting at Valdimah Park.
- Solar PV: A good base load each and every day makes solar viable compared with say, pumping for irrigation.
- Expansion plans: There are a number of energy-efficiency design considerations for Justin as he contemplates his new sheds. These include installing VSD controllers with accompanying control system versus retrofitting his current sheds, his choice of materials for insulation, and designing the roof line to optimise ventilation and reduce heating and cooling loads.
- Biogas: At present, implementating biogas facilities at a single site is economically unfeasible, but installing aregional biogas facility is worth considering, especially where there are a large number of existing sheds with plans for increased numbers over the next few years within an electricity-network-constrained area.
Figure 2: The biggest energy user is heat at this shed powered by LPG. Could there be a cheaper gas available than LPG, like biogas for instance? Lighting surprised many as the “dark horse” in the audit!
NSW Farmers
Solar photovoltaics set up a lifetime of cost savings for chook shed
Valdimah Park has several of the essentials required to support a strong business case for solar PV, including a vast roof space with more than 3,000m2 per shed and a sizeable daily peak load that varies from 20kW in winter to 60-70kW through summer, and that aligns well with daylight hours. The business case for new sheds should compare operating costs with and without solar over the life of the shed. Solar panels could be added to accommodate additional load from eletric radiant heaters, should the rise in gas prices justify such an investment.
If we add biogas to the mix, additional work will need to be done to ascertain the relative costs of biogas-fired heating (with the co-benefit of waste management) and solar PV. With any combination of biogas and solar, and perhaps battery storage, it would be reasonable to assume a 20-year life of low-cost energy; however, the question of payback periods remains unresolved at this point in Justin’s journey.
Figure 3: Solar could provide 40% of the electricity load for this farm and around 20% of the gas load with conversion to radiant electric heaters. Batteries could make a grid connection redundant especially with 2 backup generators to mange any supply risks
NSW Farmers
Optimising ventilation control saves money and improves growing conditions
At Valdimah Park, fans are turned on and off automatically to get the right level of ventilation, but at the cost of reducing internal temperature (inside temperature is reduced by 1°C for every 0.5m/s that wind speed is increased as advised by Justin). As the speed of the fan is not controllable, we get the right amount of ventilation but with an excessive reduction in temperature, which increases the heating load.
Energy savings could be achieved by reducing the speed of the fan to the desired ventilation point.
For example, reducing fan cooling by 10% reduces energy consumption by up to 27% (go to our fan factsheet for more detail). Note that implementing these savings is more complex for Justin, as it would require his current shed management control system to be supplemented or upgraded to accommodate the VSD controller.
Approximately $1,000 in savings per year across five sheds can be achieved, but more important are the co-benefits that arise from having better speed control.
“If we can control the fan speed in smaller increments, we can reduce variations in temperature, reducing risk to our birds, keeping them healthy and comfortable as well as keeping their growth rate on track,”Justin says.
Additional savings are achieved when excess ventilation is avoided, as the shed’s control system reacts to the lower temperatures and fires up the gas heating to return the temperature to ‘normal’.
If Justin does not find the option of retrofitting the existing sheds practical, installing variable speed drives would be a must in any new shed design and control system he considers.
Ground-coupled heat exchangers could help achieve cost savings for heating
Valdimah Park’s biggest energy cost is the purchase of the LPG used to heat the sheds. Moreover, the current environment for gas markets suggests that this cost may increase as gas prices rise to meet export price levels.
Although Justin’s sheds are already among the more efficient in the poultry industry, there may be a case for adding innovative ground-coupled heat exchangers to improve the heating efficiency of the sheds further.
How it works
In a similar way to a traditional air source heat pump (ASHP) exchanging heat with the outdoor air, a ground-source heat pump (GSHP) exchanges heat with the ground using a network of pipes called a ground heat exchanger (GHX). The slow transfer of energy, into and out of the ground, means ground temperatures remain relatively constant regardless of air temperatures during any particular season. Ground-sourced heat pumps take advantage of this consistent thermal mass to make heating and cooling more efficient, and can provide all or a portion of the required conditioning needed for a designated space.
Figure 4:Ground-Coupled Heat Exchanger used to condition large dwelling (left). Tubing network being installed (right)
GeoExchange, 2014
Ground-coupled heat exchangers are not a silver bullet but they do hold promise as a means of reducing heating costs, and could offer various ancillary benefits, such as:
- Reducing CO2 levels. Current gas heaters in the shed release CO2 and therefore increase ventilation requirements, increasing heating/cooling costs.
- Reducing moisture. Gas heaters also introduce moisture to the shed. Reducing gas usage can reduce moisture content so that litter is able to absorb more waste and thereby reduce ammonia levels.
- Better control of cooling. Heat-pump cooling will be a higher energy cost than evaporative, but will reduce water usage and increase yield, with better control.
- Conditioning powered by electricity. Pumps and refrigeration systems for cooling and heating run on electricity. This means that the energy can be supplied from a PV system to result in compounded savings.
Many of these benefits also hold great potential for improving bird health and thus for reducing mortalities.
This opportunity is currently under investigation and could move forward as a retrofit for Justin’s current sheds or as a new system in his newer sheds, if the case for it holds up.
Lighting retrofits hold promise
The audit process noted that lighting, while at 4% of the overall energy consumed, accounted for almost 25% of Justin’s total electricity bill.
Typically, lighting type, time and control determine the potential cost savings. Valdimah Park has five sheds currently using industry-specific halogen lamps together with T8 linear fluorescents.
Upgrading to newer technologies can potentially strip 15% from Justin’s electricity bill (around $7,000 in savings). See NSW Farmers’ factsheet on efficient farm lighting for more information.
T8s->T5s
The new lighting technologies to replace T8s include T5s, which can be retrofitted as direct replacements (with an adapter kit), and LED tubes which, in some cases, require new fittings and should be factored into the cost and subsequent business case.
T5s, with an electronic ballast, offer a modest 30% in energy savings compared with T8s and magnetic ballast, substantially more if replaced with LED tubes. LED tubes offer the additional benefits of longer life (50,000 hours, in some cases) and less maintenance, making them ideal for installation in new sheds.
Halogen incandescents -> LED bulbs
A more efficient replacement for the 75W halogen lights Justin currently uses is also under investigation. Candidate LED lights offer prospective savings of over 70%. The impacts of different heat outputs for lights and other requirements for chook sheds need to be better understood.
LED replacement lights typically use 15-20 watts as compared to 70-watt incandescents, making LED 70-80% more efficient in a direct one-for-one replacement.
At Valdimah and for many sheds, 13 hours of lighting a day is substantially more than the hours required for a typical commercial building. Replacing halogens with LEDs holds promise to save close to 70% of the total energy required for shed lighting. Also see factsheet on efficient lighting. |
Could biogas be the future for chook sheds?
“It’s a long shot, I suppose, but waste needs to be managed and energy prices are making this business difficult for most growers,” says Justin.
The waste-to-energy nexus has a number of parameters; however, one question is fundamental: what are the opportunities presented by waste?
Some of the growers involved in the NSW Farmers energy innovation studies derive income streams from their waste in the form of fertiliser; some ‘close the loop’ and return compost and wastewater rich in nutrients to pastures; and others send their waste off-site for disposal. When Valdimah Park expands, it will have sufficient solid waste, potentially, to consider installing an on-site biogas operation to provide fuel for heating or a gas for injecting into a gas genset to produce electricity for the site.
Meanwhile, however, Justin needs to contemplate the answers to these questions in relation to his Valdimah Park operation:
- Does it have the capability, with regard to space and operating conditions, to stockpile waste on site?
This is a contentious issue in poultry and one that requires careful consideration. For instance, would soluble waste be more acceptable than stockpiling dry waste for gasification? - What level of investment would be required to set up a waste treatment plant and capture the gas?
Recent investigations in the red-meat industry suggest that $1m is a minimum; however, European examples of small-scale generation are common. - What budget and/or existing staff would be available to attend to the waste treatment required?
Often, staffing is a hidden cost. - What could be done with the resulting waste?
Fertiliser by-products and biochar are often considered as options for dealing with this waste. - Is the set-up scalable with expansion?
- Is it feasible to source an additional amount of waste (biomass) reliably from surrounding farms so as to achieve greater economies of scale?
Outcomes
Investing in a 38kW solar PV system, optimising ventilation to reduce heating load and upgrading T8s to LEDs will deliver $21,000 in combined savings. A further $22,000 in opportunities is under investigation, as is the option of making 100% savings via renewable energy (biogas, solar and storage combinations). |
Figure 5: Expected energy savings from continuing implementation of projects at Valdimah
NSW Farmers
Planning for expansion and energy self-sufficiency
Renewable energy generated on-farm will underpin future productivity gains at Valdimah Park
Justin will continue to explore different combinations of generation and energy efficiencies to deliver short-term cost savings and to inform the design of new sheds to enable him to exploit the savings on offer.
Over the short term, he’ll explore the option of solar PV and possibly commission it, using a Purchasing Power Agreement (PPA) to facilitate financing. He’ll also look at installing VSDs as well as a lighting upgrade, for potential savings of around $7,500 with a payback period of 3-4 years, if the technologies can be adapted easily to the current control system.
Long-term opportunities Justin will consider include installing a ground-sourced heat exchanger and constructing a local or on-site facility to generate biogas from waste. These, combined with solar PV and perhaps a few batteries, could provide 100% of the power required at Valdimah Park.