Rejigged tariffs and equipment fixes to boost Riverina dairy farm's bottom line
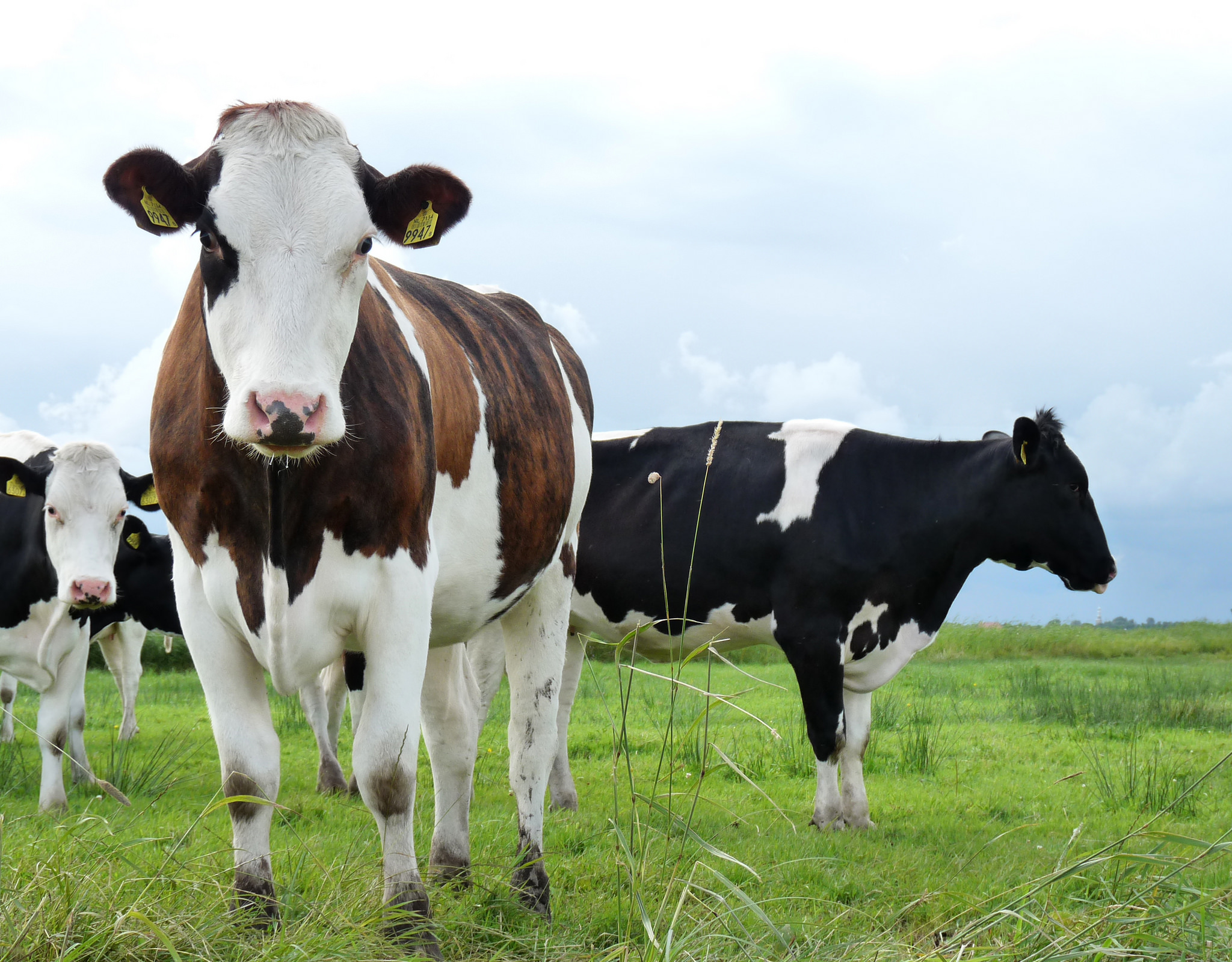
Dairy cows: an energy audit of Carramar dairy farm in the southern Riverina showed that renegotiating their electricity tariffs was a quick, zero-cost fix that could save them more than $1,700 a year.
WSPA International, Flickr CC
An energy audit of Carramar dairy farm in Womboota, near Deniliquin, New South Wales, found that significant savings could be made by renegotiating the electricity tariff for the property’s water pump. Other fixes deemed worth considering were optimising the performance of its power-hungry plate cooler, recovering waste heat from the chiller and installing LEDs.
The energy audit, which took place on 23 March 2016, examined the energy consumption patterns and current and likely future needs of the Carramar dairy operation in Womboota, in the southern central Riverina, not far from Deniliquin.
The audit, arranged by NSW Farmers and funded by Australian Dairy Farmers (ADF) using methodology consistent with an AS 3598 Level 2 Energy Audit. established the operation’s baseline energy consumption in relation to industry benchmarks for dairy sheds; analysed the property’s energy use; and pinpointed areas in which there appeared to be potential for energy and cost savings.
Energy use in Carramar’s dairy was measured, as was the performance of dairy equipment and the provision of hot water, lighting and cooling to both dairy and main household.
The audit also examined the business’s energy tariffs and looked at current energy use on the property, including on-site solar photovoltaics, solar PV pumping for the dairy shed, and the energy consumption of on-farm residences.
Opportunities to improve energy-efficiency
The energy audit identified a number of opportunities for Carramar to improve the energy-efficiency of its operations, in and outside of the dairy.
Some were seen as worth implementing as soon as practicable; others, deemed cost-ineffective in the short term, were recommended for review and possible implementation down the line.
Energy-efficiency priorities
Projects recommended as worthwhile and cost-effective included:
- changing the water-pump electricity account to avoid high service fees;
- optimising the performance of the plate cooler;
- recovering waste heat at the dairy’s chiller; and
- upgrading to LED lighting.
The energy audit team recommended that Carramar’s management implement some or all these measures as soon as is practicable so that they can start reaping the benefits.
Potential future options for improving energy-efficiency
It was suggested that Carramar’s management reconsider the energy-efficient (but not currently cost-effective) options listed below at a suitable future time, such as when old equipment needs replacing
- installing large-scale solar-powered water pumping;
- replacing the chiller unit (rather than retrofitting it with an HCU);
- installing reverse-cycle air‐conditioning in the main house; and
- replacing the old ceiling fans with energy-efficient ones in the main house and shed.
The farm's energy use
Baseline energy consumption
The following table shows the energy consumption across the whole farm in 2015 (with some extrapolations due to estimated and/or missing bills). Note: ‘fuel usage’ may not reflect the exact year of consumption as fuel is stored onsite.
Electricity |
309 kWh/day 1,113 MJ/day |
$26,200 | Includes 3 separate accounts: dairy opera ons (inc staff house), main house (inc solar), and electric pump. |
LPG | 11.4 L/day 295 MJ/day |
$3,250 | for hot water pre‐heating |
Diesel | 64.6 L/day 2,496 MJ/day |
$30,000 (before tax credits) | For diesel irriga on pumps and general farm vehicle use. |
Unleaded | 9.3 L/day 319 MJ/day |
$4,300 (before tax credits) |
|
Energy benchmarks for dairy farms
The following table shows the average energy usage of other dairy farms in the region (Dairy Australia, 2015) and for the Carrreras’ property. This data covers only dairy-shed operations, not operations across the entire farm.
The Carramar dairying operation consumes about 35% less energy than the regional average, so it’s already ahead of the game.
Murray dairy region average | 51 kWh | $10 |
The Carrera property | 33 kWh | $7 |
Total farm energy consumption
The chart above depicts total energy usage (content) at the farm.
Diesel fuel, used for vehicles and irrigation, accounts for the largest share of energy used on-farm.
Carramar’s electricity use can be broken down into specific areas of operation, as shown above.
Calculations were based on:
- bills for three separate electricity accounts held by the site;
- a sub‐meter reading for the staff house; and
- output data from the solar inverter at the main house.
Energy use by dairy-shed equipment
he final chart (above) details typical energy consumption of key equipment used in Carramar’s dairy shed.
- ‘Pumps & motors’ includes water-supply pumps from storage tanks, the milk pump, compressor, sludge pump, vat wash, feeders, agitators, auger motors and other dairy equipment.
- ‘Refrigeration’ refers primarily to the operation’s main milk chiller, the single biggest energy-user on site.
- ‘Hot water (electric)’ refers to the electric storage tank component of the dairy’s hot-water usage.
- ‘Hot water (LPG)’ is the instant gas component of the dairy’s hot-water usage.
- ‘Lighting & other’ includes the shed lighting, computer and ventilation fans.
Energy-efficiency and cost reduction opportunities in the dairy
Although Carramar’s dairy operation is already relatively energy-efficient, several opportunities were identified that would help reduce operating costs and improve efficiency further.
1. Changing the water-pump electricity account to avoid high service fees
The electricity account servicing the dairy’s electric water-supply pump now has a $6.25 per day ($2,281/year) service fee associated with it, representing almost half the bill cost and driving water-pumping costs up to $5/ML (previous costs were around $3/ML).
If the existing retailer (Red Energy) lodged an application with the network company to revert to the old tariff structure, this would make the dairy’s fee the same as that of the main household account (service charge around $1.40 per day). There’s no cost to apply; if rejected, the Carreras can explore other options to avoid this fee – such as running power to this pump from another supply point and closing the existing account, for instance.
2. Optimising the performance of the plate cooler
The audit team determined that a minor improvement in the performance of Carramar’s plate cooler could reduce the load on the dairy’s chiller substantially, in turn reducing energy costs.
It is recommended that milk entering the vat should be only 2‐3˚ C warmer than the supply water entering the plate cooler. If it enters the vat at temperatures routinely warmer than that, there’s an opportunity to boost performance and energy-efficiency by upgrading to a larger unit or adjusting the current one’s performance (e.g. its water-to-milk flow ratio, etc).
3. Recovering waste heat at the chiller
A heat recovery unit uses the waste heat from the chiller plant to pre‐heat hot water to around 60˚ C. On this property the savings from this measure would come from reduced (or completely eliminated) usage of LPG pre‐heating.
HCU costs vary depending on the supplier and system configuration; typical costs are shown in the summary table. Retrofitting the existing unit with an HCU is an option, but a full chiller system upgrade would likely be more appropriate (as explained further in the following section).
Preliminary pricing was obtained from two companies deemed suitable for Carramar’s needs: Barry Brown & Sons; and Thermal Recovery Systems.
4. Upgrading to LED lighting
Although lighting accounts for only a small percentage of Carramar’s total dairy-shed power usage, its efficiency could be improved across the property and this is a relatively cost-effective fix.
Recommended lighting upgrades include:
- upgrading fluorescent tubes in the dairy shed to LEDs for an estimated 50% energy saving;
- upgrading the remaining shed floodlight to LED (80%+ energy saving); and
- upgrading all bulbs in the household (halogen downlights, screw-ins, bayonets) to LEDs (80%+ energy saving).
Cost-benefit analysis: priority energy-efficiency projects
As detailed in the table below, the NSW Farmers' energy audit identified several cost-effective measures with potential to improve the energy-efficiency of Carramar's operations.
Changing the water-pump tariff - an easy fix, for zero cost - would save Carramar an estimated $1,700 a year.
Optimising the performance of the dairy's plate cooler by say, 1˚C, would cost an estimated $500, resulting in significant energy savings of around 2,000 kWhr/year. It would also save the business around $600 p.a. in energy costs, with an easy payback period of less than a year.
Recovering waste heat from the dairy's chiller would save 29,930 kWhr/year of LPG, and would cost a hefty $12,000, with savings estimated at nearly $3,000 p.a, it would pay for itself in four years.
Upgrading to LED lighting across the property at an estimated cost of $780 would save 2,546 kWhr/year in power and $764 p.a, giving it a payback period of one year.
1. Change water pump electricity account to avoid high service fees. | -- | -- | $1,700 | -- |
2. Optimise the performance of the plate cooler (eg. for 1˚C improvement). | 2,000 | $500 | $600 | 0.8 |
3. Recover waste heat at the chiller (savings are from LPG, not electricity). | 29,930 | $12,000 | $2,993 | 4.0 |
4. Upgrade to LED lighting (various locations) | 2,546 | $780 | $764 | 1.0 |
Potential future energy-efficiency projects
The following measures were deemed worth considering down the track for their potential to improve the Carramar operation’s energy-efficiency, but may not be cost-effective at present.
Large-scale solar water pumping
Directly coupled solar PV water pumping may in time become cheaper than grid power and diesel-driven pumps. Already, large-scale solar water pumping can achieve costs as low as $5/ML (levelised over 15 years).
With grid-electricity and diesel-powered pumping on the Carramar property currently costing a similar amount, changing the technology was not viewed as economically viable right now but would be worth reconsidering down the track, especially if new pumps are to be installed on parts of the property not currently serviced by existing diesel or electric water pumps.
Replacement chiller unit
Although a heat recovery unit retrofit is an option, replacing the chiller unit would likely prove more cost-effective long-term as old refrigerants become costlier to replace and more modern chillers incorporate HCUs as standard.
Next time the dairy’s chiller needs a big upgrade, consider replacing the entire system rather than retrofitting a HCU to the existing one.
Reverse-cycle air‐conditioning for the household
In the property’s main house, cooling is provided primarily by a ducted evaporative cooler; heating by a wood-burning stove. Both can be costly to operate particularly when indirect costs (water pumping, labour) are considered as well as direct energy usage.
As the household has a relatively large (5kW peak output) solar PV system, a split-system reverse-cycle AC system, used sensibly and not oversized, would be more cost-effective than either existing option.
Installing such a system would enable better use of solar power generated onsite – effectivly worth $0.30/kWh, whereas power exported to the grid is now rebated at only about $0.10/kWh.
Energy-efficient ceiling fans for main house (and shed)
The main household and dairy shed are cooled by conventional ceiling fans, an efficient form of cooling – except that now, more energy-efficient options exist.
Whereas an old ceiling fan may consume 50-100 W power, modern DC-motor ceiling fans (such as Aeratron) use just 10-20 W to create the same amount of air movement.
When the existing fans wear out, updating them would be worthwhile.