Insights provided by fuel and electricity monitoring drive energy plans for sheep farm near Conargo
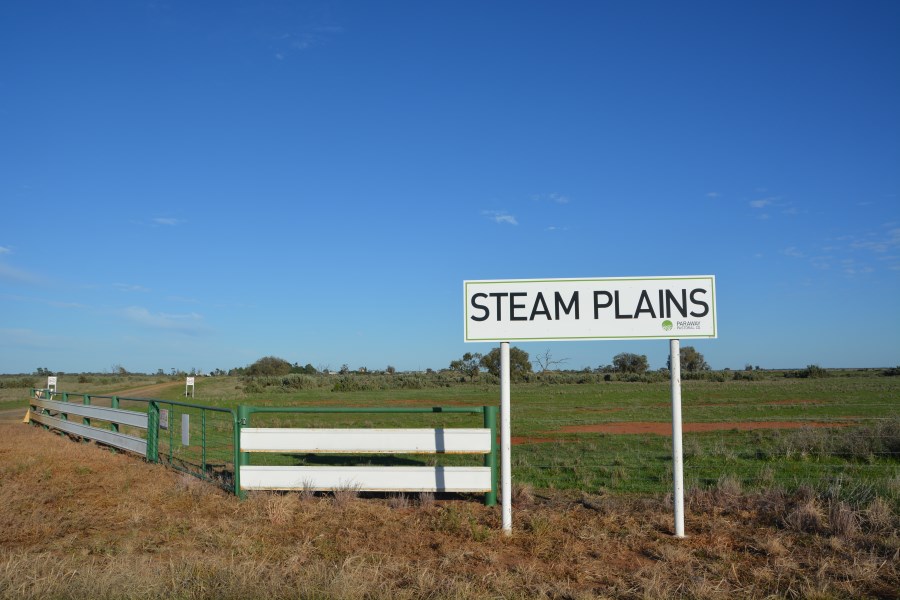
[Click here to download a PDF version of this information paper]
Approximately 40% potential energy savings were discovered from on-site generation using a combination of solar and wind. But how will the business case stack up? Monitoring and understanding energy usage provides the key.
Steam Plains is situated 35 kilometres north of Conargo in the Western Riverina district of New South Wales. At 45,834 hectares, it is one of the largest sheep properties in the region.
In addition to breeding Merino sheep, Steam Plains runs EU-accredited cattle and operates cropping enterprises including winter cereals and oil seeds.
The property’s rich black soils and well-developed irrigation system make it well-suited to a range of dual purpose cropping activities across all seasons.
Magnus Aitken describes the importance of managing energy, “Our plans include making sure the economics are right: reducing maintenance costs and raising revenue levels. Energy savings can certainly help us with the first two, as well as contributing to better margins as we lift revenues.”
With a focus on continuous business improvement, Magnus was interested in an assessment of energy savings opportunities with the NSW Farmers Energy Innovation program.
Steam Plains’ energy profile
Energy is used mainly for pumping: 80% is used for irrigating crops and 20% to provide water for stock.
Each year the property uses approximately 142,000kWh of electricity, 300,000 litres of diesel, 55,000 litres of LPG and small amounts of petrol. The energy breakdown is shown inTable 1 , below.
Table 1: Steam Plains’ energy use by type
NSW Farmers
The farm’s largest energy expense is running diesel pumps to lift and distribute ground water, mainly for irrigation.
Table 2: Energy use by type and purpose
NSW Farmers
Figure 1: Steam Plains’ energy use by type and purpose
NSW Farmers
Cost reduction opportunities
The audit conducted by NSW Farmers and their team found that Steam Plains was a property with well maintained infrastructure and very few obvious energy saving opportunities. The energy-efficiency and cost-saving opportunities that were identified are listed below.
Table 3: Full list of opportunities with 5 priority opportunities highlighted
NSW Farmers
Magnus decided to lead with energy monitoring of both fuel and electricity to inform his decisions about investing in on-site generation , fuel switching between gas and diesel, and voltage and power factor improvements.
Constant monitoring of fuel usage reveals cost savings opportunities
Blended fuels require close monitoring to exploit cost savings. Minimising spend on infrastructure can maximise your flexibility with alternative fuels. At Steam Plains, a close eye is kept on diesel and LPG prices. Around 8 years ago, the decision was made to use LPG / diesel injection for the main bore pumps, allowing blending of a small percentage of LPG with diesel to achieve the same or better output from the engine. Savings are achieved primarily as a result of the price differential between LPG and diesel. Some suppliers claim improvements in efficiency, and Magnus has seen evidence of this at Steam Plains.
Using diesel only in his engines, he was using approximately 1,000 litres per day. After switching to a blend of diesel and LPG, he had reduced his total fuel usage to 900 litres (600 litres of diesel and 300 litres of LPG).
A review of most recent pricing and savings using the NSW Farmers energy calculator revealed that despite these total fuel savings, Magnus was now only achieving a marginal benefit, due to the fact that LPG prices have been rising and are well above diesel prices. Any increase in LPG costs (~5-10c/L) would likely result in eliminating any additional cost benefit from this blending process. However, historical pricing meant that the decision at the time had saved Steam Plains $200,000-300,000 in diesel costs over that 8-year period.
If the price rise occurs and Magnus decides to cease LPG injection, the structure of the supply arrangement means that the only sunk cost is the blending kit (<$5-10k), as the tanks can be removed. His pumps can continue to operate on diesel.
Figure 2: Fuel monitoring records can be used to set and check fuel use per hectare when you supply fuel to contractors. Saving 50 cents per hectare when you have 10,000 hectares or more to sow, harvest or spray might cover your seed or chemical bill for that run!
Hytek
Monitoring electricity consumption
Magnus hoped to achieve three outcomes by tracking his electricity use:
- An understanding of the typical daily use of household electricity across 4 farm cottages, the main homestead and associated domestic bore pumps, to inform the potential sizing of any solar or wind energy solutions.
- Insight into the level of supply variation given Steam Plains’ location at the end of the electricity network line. With this information, Magnus can talk to his retailer about improving supply, the size and specifications required for on-site power conditioning, or voltage optimisation kits to deliver more reliable power supply.
- Assess whether there is further potential for savings on voltage optimisation if Magnus finds that the typical line voltage is running too far from normal.
Figure 3: Steam Plains has invested in monitoring the electricity delivered by the mains feed onto the property so that they can size new energy technologies more accurately, minimising wasted capital and realising energy use cost savings of 40% or more.
Energetics
Figure 4: Steam Plains invested in a solar bore pump with a tracking system to improve efficiency by 10%; however payback on trackers was more than 10 years. The business decision was enhanced by halving the number of trips by farmhands to this paddock to maintain and refuel diesel pumps.
NSW Farmers
Several solar suppliers have knocked on Magnus’ door with vastly different offers for between 4 and 40 solar panels. “We learnt that to pursue wind and/or solar we needed to better monitor the variability of our power onto the farm. So we invested in power conditioning equipment, stabilising our power and helping us to size our solar system to power our pumps rather than compensate for uneven supply.” Magnus Aitken, Farm Manager |
Energy monitoring data provides confidence in savings potential
Opportunities to reduce electricity use
If energy monitoring continues and expands, combined with improvements to the quality of the power coming onto site, additional savings of around 40% in electricity charges are available. These would be derived from a variety of efficiency implementations, such as:
- Power factor correction and voltage optimisation
This could result in savings of around 10% depending on how variable the power quality of the property is.
- Solar PV
In the not-too-distant future, energy storage may allow solar to affordably supply 40% of Steam Plains’ electricity.
- Wind power
Magnus observed that the average wind speed might be sufficient to generate power from a wind turbine. However, research into local average wind speeds from the Bureau of Meteorology showed that nearby towns typically experience wind speeds in the order of 3-4m/s, as opposed to more suitable wind power ranges of >5-6m/s. This significantly reduces the potential overall capacity factor and resultant annual generation for a prospective wind turbine (refer to NSW Farmers’ Wind Power fact sheet for more details on how wind turbine output varies with wind speed) 1 . As a result of these lower wind speeds, preliminary system costings showed that paybacks would be in the order of 30+ years. NSW Farmers therefore advised Magnus to forgo any wind implementations for the moment.1 Note: Some wind information resources quote wind speeds at a hub height of 80m for utility-scale wind farms. However, speeds are generally lower at heights that are applicable to smaller systems (10-20m) which are more relevant to farmers.
Opportunities to reduce diesel use
Implementing fuel efficiency targets in contracts for tractor operators and inductive processes for casual operators can achieve savings in the order of $4,000 to $18,000 per year. Efficiency targets can be met by implementing various techniques and opportunities:
- Optimising ballast points and tyre pressures to the task
Research suggests optimal set-up of these parameters can decrease fuel use per hectare by up to 15%.
- Adaptive driving
Using the Gear-Up-Throttle-Down approach can deliver significant savings, especially if the tractor is underloaded. This and other techniques have been shown to reduce fuel use by around 5-20%. The biggest potential lies with casual operators (e.g. backpackers), who may not have developed a ‘feel’ for the machine or the conditions.
Figure 5: Expected energy savings from continuing implementation of the projects
NSW Farmers
Taking control of energy costs
Magnus, with the assistance of NSW Farmers’ Energy Innovation Program, will continue to monitor fuel and electricity use as the basis for investment decisions that ensure energy at Steam Plains is delivered at the best possible price per gigajoule. The fuel options considered for Steam Plains will expand and change with the market, and careful monitoring will form the basis of smart financial decisions.
Over the short term, in addition to installing new fuel measurement equipment, diesel fuel savings can be achieved by testing new fuel-use KPIs with contractors, perhaps even offering incentives for fuel efficiency. Operators can ensure that tractor tyres are adequately inflated, and that the ballast set-up of tractors is optimal for critical operations.
In the medium term, after monitoring electricity quality for a few months, a solar PV solution can be sized and installed, saving 40% of the farm’s current electricity use. Switching over existing diesel to electric pumps is also up for consideration, providing options for electricity from renewable sources, or cheaper power from the grid. However, such an option faces some considerable infrastructure and cost hurdles.
Long-term opportunities include drawing on localised solar PV to power pumps, and examining the potential to power pumps and engines using biogas or biofuel sourced from local on-farm waste or nearby agricultural operations. Such opportunities require a higher level of investment and may not be cost-effective currently; however, their development should be monitored as technologies improve and become more commercially viable.