Energy efficiency supports the viability of a family-run dairy near Wagga Wagga
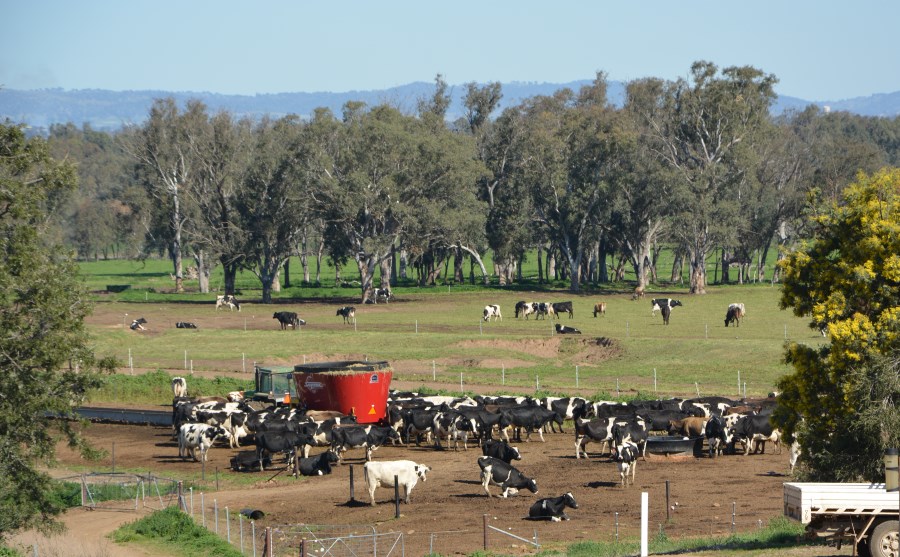
[Click here to download a PDF version of this information paper]
Price pressures in the dairy sector are forcing dairy farmers to look for ways of cutting costs to retain reasonable margins and remain viable. “We need to increase our herd and our yield to remain in business,” says Norman McCure, owner of Binowee Dairy in New South Wales. The challenge for the McCures is to achieve improvements in yield and volume at a lower cost per litre of milk. If this challenge is met, the business could not only survive but thrive, providing sufficient motivation for taking on the additional risk and hard work that the expansion will entail.
An investigation into more efficient hot water and refrigeration systems and the possibility of generating biogas on site may lead to further options for optimising Norman’s investment and delivering an estimated 30% increase in production.
The McCure family has been farming for many years. Recently, they entered the dairy business with their property Binowee. The dairy is home to around 500 cows – Holstein, Jersey and Swiss – 400 of which are milked twice daily. The cows spend most of their time grazing on pastures on the property, or in nearby pens, eating silage and grain. The McCures’ long-term plan is to expand the size of their operation to around 700 cows, with 500 of them milked thrice rather than twice daily, which may necessitate operating the farm as a feedlot with additional sheds and pens. This will change the nature of land use on the property.
Implications of expansion
In order to milk more cows, more often, the McCures will need to produce more feed and deal with more waste. This presents them with a dilemma, as the dairy is located close to other properties and communities that could be affected by all this waste. With this in mind, Sheila and the family are keen on exploring the possibility of using cow effluent to generate methane-based energy on site. Although installing a biogas conversion plant would involve a significant capital outlay, the opportunity to invest in bio-mass energy could provide a long-term solution to waste disposal and the farm’s energy needs.
On-farm energy
Binowee Dairy already has a 10kW solar PV array sited on top of the milking shed. It was installed as part of the ‘solar bonus scheme’ in 2010 but Sheila reports that the amount of energy generated by the system seems to have decreased since. The system is not visible from the ground, and there is a possibility that dust from the shed could be affecting its operation.
High energy costs, possible solutions
A dairy is an energy-intensive operation. Electricity is needed to run milking machines, pump water for irrigating fields, run cooling tanks to keep milk chilled, heat water for cleaning sheds and provide light in the early morning hours (when cows are first milked for the day). NSW Farmers and Energetics identified a number of ways to reduce these high energy costs, including strategic opportunities around biogas and expansion of Binowee’s existing solar PV system. In the short term, the McCures can boost their farm’s energy efficiency by reducing the electricity load and minimising the size of any on-site ‘energy generators’. This could include installing more efficient lighting and a larger plate cooler; optimising the temperature set points for milk storage; and targeting electricity discounts to ensure they are paying the lowest rate available. Some of these solutions involve large capital expenditures, and will vary based on the needs of the property as it grows. Investigation is ongoing but all parties involved are hopeful that implementing some or all of these solutions will help to bring down costs, making Binowee more efficient and profitable.
Binowee Dairy’s energy profile
The farm’s largest energy expenses are electricity, used to power the pumps that distribute water around the property; refrigeration for milk storage; and hot water for cleaning.
Table 1: Binowee Dairy’s energy breakdown
NSW Farmers
Table 2: Binowee Dairy’s energy breakdown by end-use purpose
NSW Farmers
Figure 1: Binowee Dairy’s energy use ‘baseline’ by type and purpose
NSW Farmers
Cost reduction opportunities
Nine energy savings opportunities were identified by the team, with the potential to save the McCures more than $90,000 in energy costs. Four opportunities (highlighted in green) were identified for implementation in 2015 and a further three for investigation only at this stage given the planned upgrade for the dairy in 2015. These are highlighted in blue in Table 3 .
Table 3: Full list of opportunities for Binowee
NSW Farmers
In a two-hour session with the Energy Team in Binowee’s office, adjacent to the dairy, Sheila, Norm and Travis, the farm manager, discussed their business plans and energy innovation priorities. Their priorities include:
- increasing the size of their plate cooler to reduce the temperature of milk going into the vat, as part of a major upgrade to the dairy;
- installing solar thermal hot water as part of a major upgrade for the dairy;
- running a ‘turn off’ campaign for the yard lights, as part of an energy waste awareness program for staff;
- exploring the viability of generating biogas from shed wastewater for a cogeneration system with waste heat recovery for hot water; and
- investigating the business case for installing a 3.5kW solar PV system for pumping water to stock and domestic areas; and
- investigating the business case for installing a 55kW solar PV system for the whole property.
Cost savings have already started
Sheila and Norman have already secured a better electricity rate, with a discount, by returning to their original electricity supplier after a short stint with a new retailer. This change has saved them around $5,000 immediately.
The McCures had thought of installing timers for the yard lights needed in the early mornings but instead, they’ve been more diligent in communicating to staff the need to ensure outdoor lights are switched off when they’re not needed.
Longer-term opportunities involve expanding solar generation on the farm as well as biogas production, should the shift to feedlots eventuate. While these energy-generation options are being costed, the McCures’ focus will be on increasing yield, volume and efficiency via a major upgrade of the dairy.
Another quick win will involve the refrigeration system for the milk vat. Changing the temperature of the vat by 1-2 °C won’t result in significant savings – an estimated $244 per annum. A better solution, and one the McCures are considering, is to convince the processor to pick up the milk around 8am instead of noon, Sheila explains.
“This means that the milk won’t be as cool, as it would only be in the vat for 30 minutes before going in the truck; however, it will save four hours a day of cooling costs for us if they agree to the change in pick-up time,” she says.
The McCures are currently negotiating earlier pick-up times with the processor; a positive response will more than likely depend on what milk temperature is acceptable at the time of pick-up, and on potential scheduling benefits or other benefits for the processor.
Upgraded milking system
Given the business imperative of increasing the volume of milk produced on the farm, the McCures have decided to upgrade their main milking equipment. The upgrade will accommodate more cows, and more milk per cow. The dairy expansion and upgrade work, expected to cost $1.5 million plus, will include:
- new pipework, going from 2-inch stainless steel to 4-inch stainless steel pipes, which will deliver better efficiency and greater flow with reduced energy use;
- new motors and pumps – for motor sizes below 5.5kW, high-efficiency motors are often 4-7% higher in efficiency compared to standard motors;
- a new, larger cooling plate delivering further energy savings (though if earlier milk pick-up goes ahead, the savings from a larger plate will be less); and
- new, automated ‘cups-off’ that release automatically – these will also save energy, as they cease to pump automatically once they disconnect. Currently, this is done manually.
The McCures have also considered installing a new solar hot water system but have decided not to complicate the system further and instead secure savings from using more of their power during off-peak periods. All the new equipment for the upgrade will comply with the current industry standards for such equipment.
A larger plate cooler saves almost $1,000 a year and pays for itself in around two years
A significant amount of energy is used to cool the milk from the cows, which starts off at around 23 °C, to 4 °C at the vat. As an intermediate cooling stage the McCures have a small plate cooler in which bore water is used to cool the milk to around 20 °C before it enters the vat. The McCures have decided to include a larger cooling plate in their planned dairy plant upgrade to further reduce the cooling load in the storage vat, which should save them around $1,000 a year after the planned expansion. Plate coolers are very efficient at taking the heat out of milk (typically around 23 °C at the cup) before it arrives in the vat, which stores milk at around 4 °C. Plates are most cost-effective when there is cheap, cool water available.
Figure 2: The plate cooler pre-cools the milk from the cows (typically around 23°C ) to within , ideally, 2 degrees of the temperature of the water running past the milk vein. When it arrives in the vat the cooling load is reduced – the alrger plate saving an additional $1,000 per year on vat cooling costs.
NSW Farmers
Solar hot water systems for the dairy and vat
In the absence of recovering waste heat from compressors or other sources nearby, solar PV can be a cost-effective way of heating water. At present, the McCures have a 10kW solar PV system, which provides electricity for general use at the site, offsetting the amount of power required from the grid. These arrays are earning income under the NSW Solar Bonus Scheme Feed In Tariff, due to expire at the end of December 2016. The McCures want to ascertain the best options available to them after the tariff ends.
As part of the upgrade, the McCures have opted to rely solely on electric water heaters; however, solar hot water systems have been shown to result in substantial savings for dairies across Australia (Dairying For Tomorrow, 2012).
Evacuated-tube solar hot water systems to provide hot water for cleaning at high temperatures (80 °C or higher) are increasingly common within the dairy industry. Binowee Dairy requires 500 litres of hot water per day, on average, at temperatures of between 35 and 80 °C, for the following tasks:
- cleansing the milking machines twice a day and again, using special cleaning agents, once a week;
- a weekly caustic hot wash using special cleaning agents; and
- washing out the milk vat every second day.
An evacuated-tube solar hot water system could be designed to include a new storage tank with enough capacity to service the planned expansion of the herd and thrice-daily milking regime. The insulated round-tubes design permits water to be heated effectively in cold as well as warmer locations. Automatic controllers maintain optimum temperatures and are supported by an electric booster element that can be limited to access off-peak electricity if required. The evacuated tubes are relatively light and could be supported by the existing roof.
These systems are also made more affordable through the provision of renewable energy certificates as part of the Renewable Energy Target (RET). The savings from such a set-up could equate to more than $100,000 over the estimated 10-year lifespan of the system.
Figure 3: Evacuated tubes for solar hot water in the dairy
Victoria DEPI, 2015
55kW solar PV saves over $16,000 year on year for at least 14 years after the system is paid off
Figure 4: Solar can be sized to service the dairy’s energy needs during sunlight hours. Batteries can extend the usage times of solar-generated power, especially for morning milking, heating and cooling and for peak-hour consumption in the late afternoons.
NSW Farmers
With an investment of close to $100,000 that will likely save the McCures only around $16,000 a year in electricity costs, they are not rushing into this option, especially as the capital they have available is earmarked for the dairy upgrade.
Outcomes for Binowee Dairy
Figure 5: Expected energy savings from continuing implementation of projects at Binowee Dairy
NSW Farmers
Quick wins that have been implemented at Binowee include better lighting control in the yards of a morning, and electricity discounts netting savings of more than $3,000 p.a.
The next wave of medium-term savings will come from negotiating earlier pick-up times from the vat, reducing the dairy’s cooling load, and as a result of the dairy upgrade (with savings accruing from the solar hot water, a larger cooling plate, and more efficient motors and system configuration).
The greatest long-term savings available at Binowee – perhaps as much as 50% of electricity costs – will be realised from solar PV and, if the McCures are sufficiently motivated by the business case, biogas, which could offset a further 40% of the farm’s energy use, leaving just 20% of electricity delivered from the grid.
MORE INFO ON PLATE COOLERS & SOLAR HOT WATER |
Dairy Australia How-effective-is-your-plate-cooler? NSW Department of Primary Industries Solar hot water for dairy shed Apricus Solar hot water – Wallalong Dairy Case Study AgInnovators |