Energy audit leads to substantial savings for Dubbo dairy enterprise
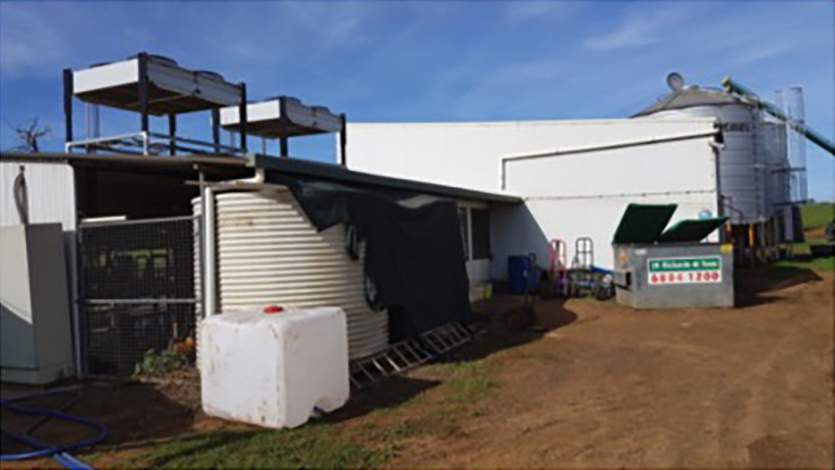
A recent energy audit looked at the energy needs and consumption patterns of the Skinner Partnership’s dairy operation in Dubbo, NSW.
The audit, arranged by NSW Farmers and funded by Australian Dairy Farmers (ADF), established the farm’s baseline energy consumption in comparison to industry benchmarks for dairy sheds, analysed its energy use in various areas, and pinpointed areas in which there is potential for energy savings.
Energy use in Skinner Partnership’s dairy was monitored; this included reviewing the performance of the equipment and systems used for milk cooling, milk vacuum pumping, and the provision of hot water and lighting.
The audit also investigated the business’s energy tariffs and looked at other energy use on the property, including solar photovoltaics, solar PV pumping for the dairy shed and irrigation bores, and the energy consumption of on-farm residences.
Opportunities to increase energy efficiency
Opportunities were identified in which the Skinner Partnership could potentially increase the energy efficiency of its operations, within and outside of the dairy. Some were opportunities that were considered worth implementing as soon as practicable; others may prove to be worthwhile in the future but were viewed as cost-ineffective in the short term.
Priority projects
Energy-efficiency-boosting projects determined to be worthwhile and cost-effective for Skinner Partnership included:
- Aluminium pivot pump: The auditors recommended that Skinner investigate changing its existing pivot pump so as to better suit the regular duty point. As detailed in the report, this would cost $5,500 but would save Skinner Partnership an estimated $2,870 a year, giving a payback period of just 1.9 years.
- Milk harvesting: Installing a variable speed drive (VSD) on the milk vacuum pump (already completed) cost $8,000 but will result in estimated savings of $2,906 per year, so the payback period will be around 2.8 years.
- Shed bore pump: Explore the option of changing this pump to one better suited to its regular duty point. With an upgrade cost of $20,500 but estimated yearly savings thereafter of $5,850, the payback period on a new pump would be an affordable 3.5 years.
- Hot water: Installing heat-recovery units for the plant and vat washes – already implemented – cost $14,000, saving around $3,330 p.a with a payback period of 4.2 years.
Potential energy-efficiency upgrades
Projects the auditors viewed as not worth implementing currently but, potentially, cost-effective down the track (such as when existing equipment needs replacing), were:
- Solar PV for the dairy (milking) shed: NSW Farmers' energy audit team advised investigating the installation of a 20kWp solar PV system in the dairy, for an estimated cost of $27,000, saving Skinner Partnerships around $3,472 annually, with a payback period (at current costs) of 7.8 years; and
- LED lighting in the milking shed: Replacing the existing fluoros with LED tube lights, at a cost of $3,190, would save an estimated $39 p.a, with a payback period of 81.8 years – worth it if the old lights require replacement but otherwise not cost-effective.
Energy usage on-farm
Whole-farm baseline energy consumption
Baseline energy consumption data was obtained across the whole farm for 2015-16, as well as:
- information on total costs, obtained from the Skinner Partnership’s Ledger report;
- data on kilowatts per hour and litres consumed, calculated using the tariffs form with sample bills supplied (and noting that fuel usage may not represent the exact year of consumption due to the use of storage tanks on site);
- data on the amount of power generated on-farm from energy harnessed via solar PV and/or by solar pumps (Note: this has not been accounted for in the tables below).
Electricity |
1,827 kWhr/ day 6,576 MJ/ day |
$ 122,125 |
Includes: dairy shed, houses, shed, bore pumps, river pump, other pumps. |
Gas |
5 kWhr/ day 126 MJ/ day |
$ 1,519 |
|
Diesel |
58 litres/ day 2,222 MJ/ day |
$ 25,610 |
For diesel, for general farm-vehicle use. |
Unleaded |
35 litres/ day 1,188 MJ/ day |
$ 15,671 |
|
Baseline energy consumption in the dairy shed
The following table compares the energy consumption of dairy-shed operations at this site with those of other dairy farms in western NSW (Dairy Australia, 2015). Note that the consumption totals exclude energy used pumping water for stock and for the dairy.
Western NSW average |
46.5 kWhr |
$13.00 |
Skinner Partnership |
33.8 kWhr |
$5.20 |
Monitoring on-farm consumption: key energy sources and usage areas
The pie charts below show usage of various types of energy - electricity, gas, diesel and petrol - and their cost for the whole farm (that is, for the dairy, houses, shed, pumping, tractors and other farm vehicles).
Electricity is Skinner Partnership’s largest energy source, in terms of megajoules (MJ) of energy and dollar ($) cost.
The pie chart below depicts the energy consumed by each area of the property (house, pumping, dairy, etc), calculated in terms of its MJ equivalent.
Pumping is the largest energy guzzler on-farm in terms of megajoules consumed, with the irrigation bores the biggest single user of energy.
Monitoring energy use in the dairy: which equipment draws the most power?
The auditors analysed the energy usage patterns of equipment in the dairy on the basis of annual electricity use, basing their analyses on data from the Skinner Partnership ledger and sample bills provided; and data obtained by monitoring key circuits in the Skinner dairy for 50 days (16 September–4 November 2016).
An ‘Ausimax’ remote electricity monitoring unit was installed at the dairy, with CTs attached to key circuits, including:
- the milk cooling system;
- the effluent pump;
- the milk vacuum pump;
- various pumps for wash-down; and
- the rotary platform motor.
The chart below details the energy consumed by all this equipment.
Note that milk harvesting includes the milk vacuum pump and milk pump; and milk cooling includes the ice-bank compressor. Hot water use is zero as the heat recovery units supply all the dairy’s hot-water requirements. The dairy audit did not monitor the energy use of providing stockwater or of dairy pumping, as these were regarded as part of ‘pumping costs’ (and were impossible to itemise specifically).
Monitoring of dairy systems showed that the dairy’s largest consumer of energy is milk cooling. The costs of milk cooling can be calculated accurately, as the ‘controlled load’ is itemised separately on electricity bills. The controlled load operates the dairy’s ice bank, which accounts for 92 percent of its milk cooling costs.
Tariffs
The table below summarises the grid-electricity tariffs for which the Skinner Partnership was being billed at the time of the audit (arrived at from bills supplied).
Dairy | |||
Peak & shoulder | 24.59 | 25% | 18.44 |
Offpeak | 14.68 | 25% | 11.01 |
Controlled load 1 | 10.39 | 25% | 7.79 |
Supply | 6.27 | 6.27 | |
Houses | |||
Consumption | 21.60 | 25% | 16.20 |
Supply | 1.31 | 1.31 | |
River pump | |||
Peak | 24.59 | 25% | 18.44 |
Offpeak | 14.68 | 25% | 11.01 |
Supply | 6.27 | 6.27 | |
Bore pumps * | |||
Peak | 18.41 | 18.41 | |
Offpeak | 10.40 | 10.40 | |
Service | 8.69 | 8.69 |
NOTE: Bore pumps are on contestible billing, based on kWhr consumed, not on peak demand. Total peak and offpeak rates include energy charges, market charges, environmental charges and network charges. ‘Service fees’ include meter and other charges and network access charge.
After reviewing the tariff offers of alternative retailers, the auditors concluded that the Skinner dairy operation is currently “on the best tariff option”.
However, as total energy consumption at the dairy may be classifiable as ‘large consumption’, the auditors noted that Skinner Partnership may be able to switch to a ‘contestible’ tariff, similar to that of the bore tariff structure.
They recommended that “an energy consumer of your size ... engage an energy broker to regularly review your tariffs and contracts”, and suggested that management routinely checks deals offered by retailers.
The auditors suggested starting any search for better energy supply deals at the NSW Government’s user-friendly site for consumers, Energy Made Easy, then contacting each suitable supplier individually to get their best offers.
Other energy use
Household consumption
Energy use in the houses on the property is significantly higher than published figures, as is common on rural properties. Note that there is a bore pump attached to each house.
Data from Energy Made Easy shows that five occupants with no swimming pool typically consume 32 kWhr/day.
Actual consumption of the Skinner Partnership’s households, ascertained from recent energy bills, is around twice this amount.
Solar PV
The table below summarises solar PV generation for Dubbo, based on Bureau of Meteorology climate data.
1 kWp |
1,500 |
4.1 |
5 kWp |
7,400 |
20.3 |
10 kWp |
14,820 |
40.6 |
Solar pumping
The table below summarises the energy consumption of solar-powered pumps on the farm. The power generated and used by these pumps was not included in the analysis above.
Old Lorantz | 480 | 12.3 |
Wool shed | 500 | 8.0 |
Gully | 240 | 7.0 |
Big windmill | 1,000 | 12.3 |
Summary: Energy consumption and costs in the dairy
NOTE: Average tariffs have been calculated for the total costs for the past 12 months from the Ledger, not from current tariffs as shown in the last bills. Annual kWhrs are taken from the graph on the bill supplied.
Energy-efficient projects
The auditors reviewed several projects with potential to increase energy-efficiency at Skinner Partnership’s dairy, analysing the cost-benefits of each.
The table below details projects the auditors deemed worthwhile; and projects that are not viewed as worthwhile currently but that may be so in future.
NOTE: All costs are estimates and are indicative only. Quotes should be obtained before any work commences. Estimated savings are based on current tariffs.
Immediately
|
|||||
1 | Aluminium pivot pump | Investigate changing pump to better suit regular duty point. Estimates based on savings detailed in report | 5,500 | 2,870 | 1.9 |
2 | Milk harvesting | Install VSD on milk vacuum pump (completed) | 8,000 | 2,906 | 2.8 |
3 | Shed bore pump | Investigate changing pump to better suit regular duty point. Estimates based on savings detailed in report | 20,500 | 5,850 | 3.5 |
4 | Hot water | Install heat recovery units for plant and vat wash (completed) | 14,000 | 3,330 | 4.2 |
Possible future projects |
|||||
5 | Solar PV on dairy | Investigate the installation of a 20kWp solar PV system in the dairy. Costs and savings detailed in report | 27,000 | 3,472 | 7.8 |
6 | Lights | Replace fluoros with LED tubes | 3,190 | 39 | 81.8 |
Review: Performance of dairy equipment
Milk cooling
To check the operation of the milk cooling system, energy use for milk cooling was monitored for 50 days. The auditors found that Skinner Partnership’s milk cooling costs were “higher than average” for the comparison group (NSW South Coast) in terms of kWhr/ kL of milk, perhaps partly because temperatures in Dubbo are comparatively high.
Monitoring the main components of the dairy’s milk cooling system – the plate cooler with bore water; the plate cooler with iced water; and the chiller unit for the ice bank – showed that milk cooling in Skinner’s dairy, including the use of compressors and fans, consumed an average of 205 kWhr/day in electricity.
The estimated cost breakdown of the unit monitored is detailed below.
Ice-bank compressor | 7.50 | 2 | 7.25 | 100% | 85% | 92.4 |
Compressor fans | 0.50 | 2 | 7.25 | 100% | 85% | 6.2 |
Compressor fans | 0.50 | 2 | 7.25 | 50% | 85% | 3.1 |
Ice-bank compressor | 7.50 | 2 | 7.25 | 100% | 85% | 92.4 |
Compressor fans | 0.50 | 2 | 7.25 | 100% | 85% | 6.2 |
Compressor fans | 0.50 | 2 | 7.25 | 50% | 85% | 3.1 |
203.4 |
The milk cooling unit’s compressors are estimated to consume 185 kWh/day.
Industrial-type plate coolers can reduce milk temperature to within 1.5 to 2° C of the cooling medium (in this case, water from the bore or ice-bank), provided the water plate cooler is working efficiently and milk is cooled to within these parameters – which is the case for Skinner Partnership.
During the monitoring process, the auditors measured water temperatures of between 17° and 18° C and resulting in-vat milk temperatures of 4° C. Given that usual milk production at that time of the year is 18,000L/day, and that the plate cooler delivered milk to the milk-cooling system at 19-20° C, the ‘coefficient of performance’ (CoP) of the compressors was estimated as 1.74, indicating that:
- the plate cooler is working efficiently; and
- the vat compressor is working as efficiently as many ice-banks do – a CoP of 1.74 is typical (the normal range is 1.5-2.5).
The auditors noted that every 1° C reduction in milk temperature flowing into the vat saves about 3,500 kWhr/year in electricity, worth $300 a year to Skinner with its current tariff.
5 key considerations when installing a plate cooler
- Use the coolest water available.
- For an industrial-type plate cooler, the flow rates of water and milk should be 2:1.
- To achieve consistent matching flow, the best option is to install a variable speed drive (VSD) on the milk pump.
- Having the right number of plates is critical to effective heat exchange.
- Regular cleaning of the plate cooler is important.
Hot water
Skinner Partnership’s electricity consumption for hot water is zero: all its dairy’s hot water requirements are supplied from heat-recovery units on the ice-bank compressors.
Volume and temperatures of Skinner dairy’s hot water use for plant and vat wash are typical in the industry.
The dairy’s heat recovery units are saving Skinner Partnership about 42,785 kWhr a year, worth $3,330 annually on the business’s current ‘Controlled Load’ tariff of 7.79c/kWhr.
The auditors recommended that extra care be taken when using hot water to minimise heat losses and improve energy efficiency and that the dairy:
- checks CIP storage fills quickly;
- checks CIP procedures to ensure hot water is used immediately prior to washing; and
- ensures its CIP storage unit is well insulated against heat loss.
Milk vacuum pump
Audit results indicated that Skinner Partnership’s consumption of electricity for milk harvesting (kWhr per kL of milk) is higher than average for the comparison group, though this analysis took place before VSD were installed on the dairy’s vacuum pumps.
At the time of the audit, the dairy’s two 7.5 kW milk vacuum pumps had recently been replaced by a 15 kW unit with a VSD drive. Typically, VSDs reduce electricity consumed by 40-60% through adjusting motor speed so the pump delivers only the required vacuum.
In comparison, the dairy’s previous vacuum-pump motors (not monitored) operated only at full speed so, depending on the load on the motor and its efficiency, would have consumed between 12-15 kW from the grid.
The auditors’ Auzimax monitor tracked electricity consumed in the dairy between 16 September and 4 November 2016 and found that the 15 kW milk vacuum pump motor with VSD installed consumed an average of 75.6 kWh/day for the two milkings monitored.
Higher consumption was recorded during plant wash, lower during milking. On average, the milk vacuum pump motor used 7.32 kW.
Compared to the assumed consumption of 12-15 kW with no VSD, this represents a saving of between 39 and 51 percent in electricity consumed as a result of installing the VSD.
The auditors could find no options for further reducing milk harvesting costs, except practices such as:
- not running vacuum pumps for longer than necessary;
- maintaining vacuum pumps regularly; and
- getting them serviced by an accredited technician if anything seems awry.
Lighting
The auditors calculated the cost of Skinner Partnership’s dairy lighting based on the lighting set-up in the milking shed: six single and six double fluoro tubes and six high bays, each running 1.25 hours a day.
With the age and condition of the battens, the auditors noted, the entire unit would likely need replacing soon, and suggested installing new LED tubes and an LED high bay instead. Given the lights’ short run times, LEDs weren’t deemed worth the investment; however, the auditors recommended that Skinner consider energy-efficient alternatives next time the dairy lights need replacing.
LED tubes can save up to 50 percent of electricity used and have a life of up to five times longer than fluoros (50,000 hours compared to 10,000 hours); however, as LED light can be quite directional, it’s important to check that LED lighting would work with the milking set-up.
kW | No. | Hrs. | Rate | kWhr/day | kWhr/yr | kWhr savings/yr | Savings $/yr | Cost $/unit | Cost $ | Payback (years) | |
LIGHTS | |||||||||||
Single fluoro | 0.045 | 6 | 1.25 | 0.1577 | 0.3 | 123 | 62 | 10 | 65 | 390 | 40.2 |
Double fluoro | 0.090 | 5 | 1.25 | 0.1577 | 0.3 | 103 | 51 | 8 | 100 | 500 | 61.8 |
High bays | 0.475 | 6 | 1.25 | 0.1577 | 0.8 | 274 | 137 | 22 | 250 | 1,500 | 69.5 |
Installation | 800 | ||||||||||
TOTAL LIGHTS | 39 | 3,190 | 81.0 |
Effluent pump and rotary platform motor
Monitoring energy use at the dairy included monitoring the effluent pump and the rotary platform motor, with results indicating that both are functioning as designed.
The effluent pump, which has an 11 kW motor and runs for approximately four hours a day, was found to consume an average of 31 kWh/day.
The auditors calculated that an 11 kW motor operating at 70 percent load with a 90 percent-efficient motor for four hours would consume 34 kW/day – making Skinner’s an efficient system.
The dairy’s 3 kW rotary platform motor, running six hours a day, consumed an average of 17 kWh/day. A 6 kW motor operating at 90 percent load with a 90 percent-efficient motor for six hours would consume 18 kWh/day, meaning this equipment is also running at high efficiency
Irrigation from bores
Basic operational data collected from the property’s irrigation bores during the on-site energy audit included pressure at pump/bore outlets; flow rate; kWhr consumed and kW draw. Pump specifications and depths for each bore were collected by Tim Hinds of Team Irrigation.
This data was used to conduct a ‘pre-feasibility analysis’ on existing pump performance and ascertain the cost-benefit of installing alternative pumps; the results are summarised in the table below. Note that these are preliminary results only and need to be confirmed by more detailed investigation.
It appears from the pre-feasibility analysis that Skinner Partnership’s shed bore and aluminium pivot pumps are throttled back significantly and are consuming more electricity than would pumps better suited to the duty point at that time.
Cost of power for bores
Note: all ex GST
$/year | $/year | Savings | Cost | Payback (years) | |
Shed bore pump | 24,234 | 18,384 | 5,850 | 20,500 | 3.50 |
Aluminium pivot pump | 4,570 | 1,700 | 2,870 | 5,500 | 1.92 |
100 Acre Lane pump | 14,242 | 14,242 | 0 | ||
Meter + service fees | 4,550 | 4,550 | |||
TOTAL BILLS | 47,596 | 38,876 | 8,720 | 26,000 | 2.98 |
From the farm ledger, the auditors found that Skinner Partnership spends $47,600 (ex GST) per annum on electricity for its bores; and $4,550 (ex GST) on meter and service fees.
Based on an average consumption cost of 14.6c/kWhr, a total of 295,000 kWhr/yr was used. [For the three bores: 45.6 + 26.8 + 8.6 = 81 kW in total was drawn from the grid. Hours pumped/year = 295,000/81 = 3,640 hours/year, or 10 hours/day.]
The auditors considered various options for saving energy use by bore pumps.
1. Shed bore
OPTION A: EXISTING PUMP, WITH THROTTLE
The property’s existing shed bore pump, an SP160-4a with a 45 kW motor, with throttle, at 23.4 L/sec, produced a total head (off curve) of 101m, with 38 kW absorbed (45.6 kW from grid), giving it a motor efficiency (in theory) of 38/45.6 = 81%. The pump efficiency, at the time measured, was (23.4 x 101)/38 = 62%.
OPTION B: EXISTING PUMP, NO THROTTLE
The auditors determined that the existing pump with NO throttle would deliver 35.2 L/sec at 87m total head, drawing 40.5 kW absorbed (50 kW from grid, with an 81%-efficient motor); and a pump efficiency of 76%.
OPTION C: PUMP UPGRADE
The third option considered was an alternative pump, the SP95-7 with a 30 kW motor, which can deliver 23.4 L/sec at 87m, drawing 28kW absorbed (34.6 kW from grid, at a motor efficiency of 81%), with 72% pump efficiency.
Costs to deliver 1 ML at 14.6c/kWhr
Hours pumping | kWhrs | kWhrs/ML/m | $/ML | $/ML | |
(a) | 11.8 hrs | 540 kWhr | 5.3 | $78.8 | |
(b) | 7.9 hrs | 369 kWhr | 4.2 | $53.9 | $24.9 |
(c) | 11.8 hrs | 413 kWhr | 4.7 | $60.3 | $18.5 |
Costs to run the existing shed bore pump, per year:
3,640 x 45.6 x $0.146 = $24,234 p.a.
Savings from installing a new shed bore pump:
Replacing (a) with (c) saves 45.6 – 34.6 = 11.0 kW drawn from the grid. For 3,640 hours pumping/year = 40,040 kWhr/year. At 14.6c/kWhr = $5,850 a year
SP95-7 with 30 kW = cost equipment = $15,500 (ex GST)
Installation = $5,000 (approximate)
Payback period = ($15,500 + $5,000)/$5,850 = 3.5 years
2. Aluminium pivot pump: SP46-6 with 9.2 kW motor
When the auditors measured this pump, the flow was unknown as its meter was not working (assumed 2.2 L/sec from curve). Pressure was measured as 430 kPa at gauge, after throttle, with 8.6 kW drawn from the grid. The pump/water depth below-ground was 35m; the total head (after throttle) was 35 + 43 = 78m.
OPTION A: EXISTING PUMP WITH THROTTLE
At 2.2 L/sec, total head produced (off curve) 78m with 6.2 kW absorbed, and a motor efficiency (in theory) of 6.2/8.6 = 72% efficiency. Pump efficiency at the time measured was 2.2 x 78/8.6 = 20%.
OPTION B: Alternative pump: SP11-15 with 3kW motor
This pump can deliver 2.2 L/sec at 78m, drawing 2.6 kW absorbed (3.2 kW from grid, at a motor efficiency of 80%) with a pump efficiency of 66%.
Costs to deliver 1 ML at 14.6 cents/ kWhr
Hours pumping | kWhrs | kWhrs/ML/m | $/ML | $/ML | |
(a) | 126 hrs | 1,085 kWhr | 13.9 | $158.4 | |
(b) | 126 hrs | 405 kWhr | 5.2 | $59.1 | $99.3 |
Costs to run the existing aluminium pivot pump, per year: 3,640 x 8.6 x $0.146 = $4,570
Savings: Replacing Option A with Option B saves 8.6 – 3.2 = 5.4 kW drawn from grid. For 3,640 hours pumping per year, that’s a saving of 19,650 kWhr per year.
At 14.6c/kWhr, that saves Skinner Partnership $2,870 p.a.
The cost of the SP11-15 with 3kW motor = $3,500 (ex GST). Installation is around $2,000.
So the payback period = (3,500 + 2,000)/2,870 = 1.9 years.
3. 100 Acre Lane Pump: SP95-7 with 30kW motor
The existing pump’s flow was measured at 18.7 L/s (67.3 m3/hr). Pressure was 770kPa at gauge; with 26.8 kW drawn from the grid. Off curve, the pump absorbs 26.5 kW = 99% efficient. Pump/water depth below ground is 50m. Total head (after throttle) is 50 + 77 = 127m.
[The auditors concluded that the 77 was likely an erroneous reading, as it was higher than the curve and higher than readings from other pump gauges. Power consumption indicates that possibly, the SP95-6 pump, which draws 22.5 kW and delivers 91m head, with 41m delivered to the system, is compatible with other pumps. If so, the motor efficiency would be 84%, which is more realistic.]
OPTION A: ASSUMED SP95-6 PUMP
At 18.7 L/s, the total head produced (off curve) with this pump is 91m, with 22.5 kW absorbed (26.8 kW from the grid). The motor efficiency (in theory) = 22.5/26.8 = 84%.
Pump efficiency, at the time measured = (18.7 x 91)/22.5 = 75%.
OPTION B: ALTERNATIVE PUMP
No alternative pump was suggested.
Costs to deliver 1 ML at 14.6c/kWhr
Hours pumping | kWhrs | kWhr/ML/m | $/ML | |
(a) | 14.85 hrs | 400 kWhr | 4.4 | $58.4 |
Savings: No alternatives were suggested.
Cost to run 100 Acre Lane pump: 3,640 hours/year x 26.8 kW x $0.146 = $14,242 + GST p.a.
Solar PV on dairy
The auditors analysed the pre-feasibility of installing solar PV for the dairy shed, noting that a more detailed review should be carried out before any solar PV installation takes place. Milking times of 5:00–8:30am and 2:00–5:30pm were adopted, with half an hour’s washdown time allotted for each milking.
The analysis estimated daily energy-use pattern in Skinner Partnership’s dairy indicated significant payback periods – of between 6.9 and 7.8 years – for installing a suitable solar PV system in the milking shed. This payback period could well improve in the near future.
The table below details estimates of electricity generated and used, with costs and savings.
Solar PV analysis
SYSTEM SIZE | COST $ | Generated | Used at dairy | % used | Fed-in | Used | Fed-in | $ saved + income/yr | Payback |
5 kWp | 7,000 | 7,410 | 4,634 | 63% | 2,776 | 0.1844 | 0.06 | $1,021 | 6.9 |
10 kWp | 14,000 | 14,820 | 7,686 | 52% | 7,134 | 0.1844 | 0.06 | $1,845 | 7.6 |
20 kWp | 27,000 | 29,640 | 13,613 | 46% | 1027 | 0.1844 | 0.06 | $3,472 | 7.8 |
Other potential energy savings
Switching off equipment
Reducing the time equipment runs can significantly reduce your energy bills. This is particularly important for large motors. The auditors suggested:
- not running milk vacuum pumps unless required;
- not continuing to pump when the tank is full and overflowing;
- switching off lights and fans when not required; and
- investigating automation.
Maintainance and replacement equipment
The auditors noted that to ensure energy efficient operation, ongoing maintenance and servicing of equipment is essential. Specifically, they advised the following:
- Service the compressor yearly.
- Clean fins on the compressor to remove dust and dirt.
- Replace damaged fins on the compressor.
- Check and replace anodes in the hot water system.
Though it may be cost-effective to replace existing equipment to improve energy efficiency, they contended, the equation changes when existing equipment is at the end of its useful life and needs replacing. Then, the comparison is between the incremental cost of an energy-efficient option compared to the basic option.