Electricity or diesel for irrigation pumping the key energy consideration at a mixed-farm enterprise
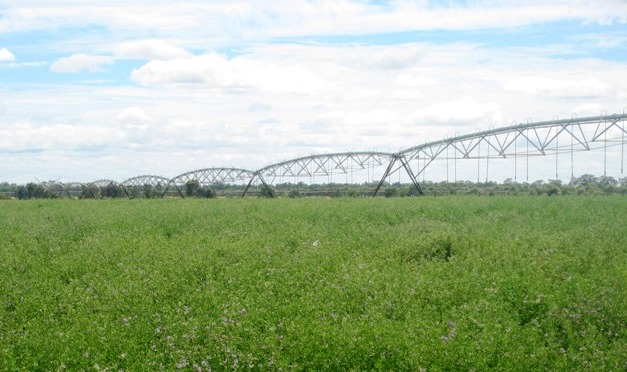
[Click here to download a PDF version of this case study]
Killeneen is a 2,700-acre cropping and cattle property north-west of Albury, New South Wales, with 60% of the land dedicated to cropping and 40% to stock. Crops grown here include winter cereals such as canola and summer irrigated crops including lucerne, corn and beans. The farm’s energy costs are dominated by that of diesel fuel for bulk water pumping. Killeneen owner-manager Derek Schoen is keen to electrify his irrigation system. He engaged with the farm energy innovation program to explore the options for and potential efficiency gains from doing so.
Electric pumps preferred
Compared to diesel pumps, electric pumps are more efficient, have lower maintenance requirements and are easier to control via automated systems. They are also quieter and generally more user-friendly. For these reasons, most irrigation farmers would prefer to electrify their irrigation systems. This is not always feasible, however, due to the costs of grid connection.
In this regard Killeneen is typical of many irrigation properties in NSW. Derek would like to electrify his bulk water pumping and was interested in understanding the variables that impact the running costs of various power configurations for irrigation pumps.
In addition, he is planning to extend his irrigation system, which will require purchasing new pumps and a decision on whether to go diesel or electric.
“We are planning to use additional pivots to irrigate more country next season, so I’m interested in the business case for electric, given the maintenance and monitoring advantages.” Derek Schoen |
Derek worked with the team to examine the options in the context of his broader energy objectives for the farm.
Killeneen’s energy profile
An energy assessment was conducted for the property to establish its energy baseline (Figure1 ) and clarify the breakdown of on-site energy sources and usage.
Table 1: Killeneen’s energy breakdown
NSW Farmers
Diesel represents 90% of the farm’s annual energy bill of $53,000 ( Table 1 ), with the majority of this, around 70%, consumed by irrigation pumps ( Table 2 ).
Figure 1: Killeneen’s energy use ‘baseline’ by type and purpose
NSW Farmers
Currently, all of Killeneen’s irrigation pumps are diesel-fuelled; they range in size from 2 to 54hp. The farm’s tractors are dedicated for particular applications: a 270hp Fendt is used for sowing; a 140hp Fendt for spraying.
Killeneen also generates some of its own electricity using a 10kW solar PV array.
Table 2: Killeneen’s energy breakdown by end-use purpose
NSW Farmers
Cost reduction opportunities
The energy assessment identified five opportunities with the potential to save more than $10,000, or 20% of Killeneen’s annual energy costs. These are shown in Table 3.
Table 3: Full list of opportunities. Note: ‘UI’ indicates ‘Under Investigation’.
NSW Farmers
The Schoens are also exploring the potential of redirecting electricity generated from the farm’s existing solar panels that currently goes into the grid to another use on the property.
Comparing the potential pumping costs of the current diesel system against electric alternative
The irrigation season at Killeneen runs from September to May, with the highest demand for water occurring from January to March. Irrigating over these periods maximises the yield of summer crops and helps prepare the ground for sowing winter crops.
Killeneen gets effluent from a neighbouring piggery piped to its eastern paddock, but the volume delivered is decreasing as the piggery has internalised more effluent use.
The costs of pumping a megalitre of water using the farm’s existing diesel motor with those of pumping the same amount of water using an equivalent electric motor were compared. The costs of pumping water in this instance, using the current 30hp (irrigation) and 54hp (dam-to-pivot) diesels pumps, are summarised in Table 4.
Table 4: Comparison of diesel and electric pumping costs for Killeneen. Note: Electric system costing assumes that the installation of an additional power pole would be required.
NSW Farmers
This shows diesel pumps to be slightly cheaper to operate than equivalent electric pumps, but the amounts exclude the potential maintenance co-benefits that would result from switching over to electric.
“We have two centre pivots and we are currently assembling another using second-hand parts, in preparation for opening up more country to irrigated crops. We pay around $45 per ML for water from a local irrigation scheme and so when you add diesel, it’s closer to $60 a ML by the time it arrives in the paddock.” Derek Schoen |
Results of the Energy team’s analysis
Under current conditions, the Killeneen 54hp (40kW) dam-to-pivot pump conversion would not be cost-effective based on current usage patterns and rates for fuel and electricity (see scenario 0).
A number of alternative scenarios were examined to compare possible outcomes of converting the pump to an electrically-powered system when key factors, such as the costs of diesel and electricity, change. This will help Derek to evaluate the business case for implementing this project, should any of these scenarios become likely.
Scenario 0. Conversion to an electric system under current conditions. Currently, diesel costs $1.38/L and electricity 32c/kWh. Additional poles, transformers and wires would be required for conversion to electrically powered pumping, resulting in an expected payback period of 60 years.
Scenario 1. With an escalation in diesel price. A 300% increase in the price of diesel (to $4.40/L) would reduce the payback time of the project significantly, to 10 years (assuming the same connection costs for transformers, poles and wires).
Scenario 2. With a reduction in the electricity tariff . At present, Killeneen is on a ‘franchise tariff’ of approximately 32c/kWh; however, converting the farm’s pumping infrastructure to electricity could substantially increase electricity use (by >100MWh/yr or approx. 24,000L diesel for a single pump). In turn, this may enable Killeneen to negotiate a cheaper price for power – potentially, as little as15c/kWh or less – under a contestable electricity contract. This would result in a payback period for this project of around 30 years.
Scenario 3. With reduced infrastructure costs. If electrical poles and wires are in close proximity to the pump, there may be smaller or no additional charge from the electricity network provider for setting up a connection point. By itself, this would shorten the project’s payback period substantially, to 23 years.
Scenario 4. With increased pumping requirements. A doubling of the fuel used for pumping at Killeneen would mean that conversion to an electric pumping system would have a payback period of 42 years.
Scenario 5. A combination of scenarios 2, 3 and 4. A payback period of just six years could be possible if pumping requirements increased sixfold (by volume of water); a lower electricity tariff of 15c/kWh was obtained; and no infrastructure costs were incurred from connecting to the grid.
These scenarios and their payback periods are also compared in Figure 2 (below).
Unfortunately, with the exception of a 300% increase in the price of diesel (scenario 1), no circumstances in isolation could cause the project to have a payback period of less than 23 years.
Figure 2: Expected payback times for converting Killeneen’s main irrigation pump from diesel to an electric system under various scenarios.
NSW Farmers
Electricity tariffs: ‘franchise’ vs tailored electricity contracts If a business consumes electricity past a certain threshold (typically more than 140 MWh per year), it may be in a position to negotiate a tailored contract with an electricity retailer. Lower electricity tariffs are generally available under these contestable contracts, which can entail 30% or more in savings compared to standard ‘franchise’ tariffs. |
Should Derek decide to convert pumps sited in places where there are no existing power poles allowing access to electricity, the additional cost of installing poles and wires will in most cases blow out the payback period beyond what is reasonable, as shown in Figure 2.
Provided the pumps Derek wishes to convert have easy access to the electricity network and there is a sufficient pumping volume per year, converting from diesel-driven to electric pumps will improve pumping power efficiency and reduce costs, if the payback period is palatable. Typical efficiencies for electrical motors range between 70 and 90%, whereas diesel engines have an efficiency of just 30 to 40%, meaning that a lot of horsepower is wasted in pumping the same amount of water using a diesel motor. Other advantages of electric pumps include lower maintenance requirements and pumps that can be integrated more easily with other pump controls, such as variable speed drives, to reduce motor speed when the pumping load lessens. Electric motors do hide some indirect losses, however – along with larger greenhouse gas emissions that are not as readily apparent as those of diesel motors. The bulk of electricity in eastern Australia is generated by coal-fired power stations, which operate at an energy-efficiency conversion rate of 30 to 40% and result in large-scale emissions of greenhouse gases.
Savings from fuel monitoring
Derek is keen to install a number of fuel monitors at each of his diesel tanks and to keep a record of the diesel consumed by each application including pumping, spraying and sowing.
As a result of not having a fuel monitor, Derek has only ballpark numbers when it comes to the fuel used by his diesel pumps and tractors and would be unable to detect even major variations in fuel consumption indicative of poor operations.
Despite this lack of hard data, Derek and his employees have a very good knowledge of the volume of water they expect from each pump (e.g. the number of syphons per field).
Diesel fuel monitoring would help Derek to develop a better understanding of fuel use on site, giving him the information he needs to decide which of his pumps should be shortlisted for review, based on savings potential from retrofits and early identification of the need for maintenance work.
Review household electricity use
While the bulk of Killeneen’s energy cost is incurred by pumping water for irrigation, the household and associated storage represents about 10% of the farm’s total annual spend, or about $5,000 per year, and offers some options for reducing energy use and costs. Derek intends to review the household energy use to determine if there are quick wins to be made here, such as in ensuring items are switched off when not in use or in upgrading to more energy-efficient appliances. Appliance upgrades are generally most cost-effective when you need to purchase new items anyway: then, the additional upfront cost more than pays for itself through energy savings in the long term.
Other areas worth investigating include whether Killeneen’s routinely high electricity bills are being driven by the farm’s electric hot water system. This recurring cost could be reduced through implementing free, water-friendly practises such as having shorter showers and installing low-cost energy-saving items including aerators and low-flow shower heads. Alternatively, Derek may decide to explore costlier but less energy-guzzling alternatives to his existing hot water system such as solar, heat pump or LPG.
Making better use of the farm’s solar power
Currently, the 10kW ground-mounted solar PV system at Killeneen is benefiting from the NSW Solar Bonus Scheme gross feed-in tariff, which will cease after December 2016. Killeneen’s total electricity demand was 14,500kWh last year; most of this was daytime demand for energy for household purposes including domestic water pumping and lighting for the house and shed.
The existing solar PV system can generate around 14,000kWh of electrical power per year (or around $2,500 per quarter in electricity savings); however, the solar power generated is generally mismatched with the times of peak power use on site, leaving excess power generated during the day that could be stored for use in non-daylight hours.
Once the NSW Solar Feed In Tariff ceases, the use of energy storage (batteries) may allow the solar power generated on-farm to be used to provide 100% of the power needs of the household as well as making a small contribution towards a diesel-to-electric pump conversion, if the operating costs make this option more attractive than others for selected pumps on the property. The following tips are offered to those with on-farm solar power generators:
- Use power on farm: Maximising the use of power generated on site will result in an overall reduction in the amount of electricity consumed from the grid. A system that continues to feed into the grid after December 2016 will likely generate no payment for the power it exports, yet the farm will continue to pay 20-35c for each kilowatt hour of power it takes from the grid. Note that maximising your use of on-site power requires you to use this power as it is generated through the day.
- Feed power to the electricity grid: Currently, the tariff is up to 6c/kWh for any surplus power generated and not used on site. The actual amount is regulated and may vary a little from year to year. Note that not all electricity contracts include this option.
- Expand the current solar PV array and convert diesel motors to electric ones:Earlier analysis showed that diesel-to-electric-motor conversion is cost-prohibitive due to the new network connection costs and relatively high electricity rate. One way this can be made to work is if an expanded solar PV system is installed which can then also power a diesel-to-electric converted motor, with electricity being generated for free once the system is installed. Downsides to this scenario would be if pumping is needed only for 3-4 months a year and is typically run 24/7 for days at a time, as solar power can be generated only during daylight hours. The addition of energy storage (covered in the next section) might help overcome some of these hurdles.
- Add storage to enhance the business case for on-farm use: Installing a bank of batteries would provide much greater flexibility with respect to the time periods power can be used, allowing solar power generated by day to be used after dark rather than having to use it as it is being generated – or lose it.
Derek will monitor battery costs, predicted to become cheaper by 2016, and consider making a business decision on purchasing batteries for storing solar power in 12 to 18 months’ time, nearer the time of the cessation of the feed-in tariff. The sales of plug-in electric cars and utility-scale solar batteries is expected to drive the price of smaller battery packs suitable for mid-sized farming applications down to more affordable levels.
The 10kW solar PV system at Killeneen is probably in excess of the farm’s current household needs, and may equate to as much as 18kWh stored in a battery per night. Unfortunately, this is far less than what would be required to drive a 40kW motor such as that powering the main dam pump to the pivots.
Figure 3: Ten kilowatts of power will soon be fed into the grid with limited financial benefit for Killeneen. The farm’s current electricity load is far less than what can be generated by its solar PV system. Converting diesel pumps to electric is one way the excess solar power generated could be utilised on-farm, but the initial cost of providing access to this power (including installing poles and wires) may be Derek’s biggest hurdle.
NSW Farmers
Outcomes for irrigated mixed farm
Improved fuel monitoring in pumps and tractors, together with solar PV and a reduction in household energy use, could provide energy cost savings of just over $11,000 a year, or approximately 20% of Killeneen’s energy use.
The bigger prize, if the price of batteries continues to come down, will be the capacity to store all the power generated by the additional solar PV system, enabling access to power beyond the current six-hour window.
With this change, Derek could offset the vast bulk of his electricity costs and might then want to consider some electric applications to power the farm’s vehicles, and/or additional diesel pumps.
Figure 4: Expected energy savings from continuing implementation of projects at Killeneen
NSW Farmers
Killeneen’s energy plan
Derek will continue to explore energy-generation and energy-efficiency options that can help secure the future of his mixed-farming operation near Albury. The opportunity to go ‘off grid’ is there, but not without significant investment in infrastructure despite Killeneen’s 10kW solar PV system.
In the short term, Derek will begin monitoring the diesel and water used by his pumps and tractors (an example is shown in Figure 5, below) and will review household energy use to pinpoint any quick wins.
Figure 5: An example of an inline fuel meter
STM Australia PTY LTD
In the medium term, the business case for redirecting the power Killeneen currently feeds into the grid will be refined over the next 12 months so that when the feed-in tariff ceases, Derek has a clear view of his options and can make an informed decision about what means of power generation is likely to be most cost-effective and will best meet the farm’s energy needs.
Long-term opportunities include a consideration of solar energy storage, coupled with the existing PV system at Killeneen or an expanded array. Batteries will be the key enabler for making this energy decision feasible.
NSW Farmers will be monitoring innovation in battery storage and releasing information to support these decisions as we get closer to December 2016.